Теоретично патентоване е бързо охлаждане на телта в аустенитната състояние до предварително определена температура, последвано от стареене за време над време на изотермични разлагане при тази температура до получаване на структурата на сорбитол. На практика крайна скорост охлаждане тел, прегряване частта вход и се загрява банята по време на прехода фаза в у-желязо води до факта, че дори когато се охлажда в олово, и освен това - в аустенит се трансформира в нитрат сорбитол в определен температурен диапазон, който зависи от свойствата на проводника, и охлаждащата среда (polytermic конверсия). Следователно, оптималната температура на охлаждане баня е различен за различните охлаждащи носители и зависи не само от диаметъра на степените на тел и стомана, но също така и от температурата на нагряване, време аустенитиране и дори топене на стомана, тъй като в различни условия аустенит стабилност е малко по-различен.
Намерени в лабораторни инсталации с кипящ слой режими скорост отопление с различни диаметри тел (от 0,8 до 12 mm) и степени (U7-U12, 70S2HA, 60S2) осигуряване neobezuglerozhennoy повърхност приемане без мащаб. Това също така дава резултатите от много подробни изследвания на кипящия слой като охлаждаща среда за патентоване. Първо, върху проби в лаборатория инсталации Урал Политехническия институт и след това преминаване trehnitochnoy баня при Beloretsk металургичен завод (нагряването се извършва в обикновена електрическа пещ) се работи оптимални режими на охлаждане тел горе стомани и диаметри. Подробно сравнителни проучвания са показали, че жицата, патентованата кипящ слой не е различна от патентованото на терена и нитрат не само за механични свойства (якост, удължение резерв от пластичност и т. Д), но и на редица физични свойства (електрическо съпротивление, остатъчен магнетизъм, насищане поток плътност, коерцитивната сила). Тъй като коефициентът на топлопредаване от горещ проводник към слоя на кипене е малко по-малък от разтопено нитрат и много по-ниска, отколкото за олово, за да се получи същото скоростта на охлаждане в баня с кипящ слой температура му над температурата на олово и селитра бани трябва да избере по-ниската по-голям и по-малък диаметър съпротивление тел преохлажда аустенит. За въглероден тел (U8A стомана) с диаметър от 6.3 mm, например, най-добрите свойства се получават чрез патентоването кипящ слой (60-100 микрона диаметър корунд частици) температура от 35-40 ° С В този случай, както е показано термограма охлаждане аустенит разлагане се извършва при температура от 500-600 ° с тел, т. е. приблизително в същия диапазон като в охлаждащата нитрат с температура 480 ° с (съгласно технологията, приета от растения).
Понякога има страхове, че патентоването слой, така ниска температура може да доведе до увеличаване на количеството на остатъчния аустенит. Специални проучвания са показали, че това се случва: в резултат на топлинна енергия в процеса започва при определена температура фазов преход, температурата на тел не намалява, но дори и леко се увеличава, въпреки пренос на топлина към слоя на кипене (ако диаметърът не е твърде малка) и следователно по същество цяло аустенит разлага в сравнително тесен температурен диапазон.
При равни други условия температура оптимално охлаждане баня намалява с увеличаване на диаметъра на флуидизируеми частици.
Въз основа на резултатите, получени през 1965 г., е оформен технически проект-резба механизъм 24 за патентоване тел чрез нагряване и охлаждане в кипящ слой.
Впоследствие, въз основа на тези развития Giprometiz (Ленинград), заедно с нас, извършено в работния проект на устройството е показано на фиг. 68. Тя е предназначена за патентоване на стоманена тел диаметър 1,6-5,5 мм, непрекъснато се движи резба 24, със стъпка от 28 mm при скорост от 10-36 м / мин (вместо 6-20 м / мин на съществуваща инсталация). Общата дължина на осите на машината е 9.17 m (съществуваща инсталация има дължина от 22 м).
Устройството се състои от пещ за нагряване на телта (дължина 3.4 m светлина) и охладителна камера (дължина 4.6 m и ширина от 928 mm), разделени с преграда. Температурата на флуидизирания слой в пещта се приема равна на 950 ° С, жицата на изхода от пещта се загрява до същата температура. Температурата в охладителната камера приема, че е 60-450 ° С, в зависимост от диаметъра на проводник (напречно сечение на по-голяма трябва да бъде по-ниска). На изхода на единица проводник се охлажда до 120-430 ° С
В кипящ слой е образуван от корунд частици от 100 микрона. Пещ при условие товарни люкове и устройства за отвеждане корунд. Височината на плътен слой от корунд приема, че е 470 мм над отворите капачката. Жицата в събранието се движи на височина от 270 мм над отворите капачката и се поддържа от напречни прегради увиснала.
изгарянето на два етапа на природен газ е необходимо да се създаде не-окисляваща атмосфера се извършва само в една част на пещта, където температурата на проводника надвишава 600 ° С и евентуално неговото интензивно окисление - в т.нар II зона пещ, състояща се от три секции капачки. Капачките са разположени във всички зони на пещта в 100 х 90 mm. Вторичен въздух се подава през серия от тръби с отвори в хоризонталната равнина, разположени на височина 470 мм над газоразпределителна мрежа на стъпки от 320-400 мм. В I (като проводник) зона пещ, състояща се от три секции в ширината на изгаря схема на един етап газ. Тук жицата е сравнително студена и на практика няма интензивно своите продукти на окисление на пълното изгаряне на газ чрез изгаряне на в = 1. Този вход на пещта (1 метър) се разширява, за да бъде в състояние да донесе повече топлина, за да жицата в малка дължина. Чрез това е възможно да се намали термичният товар останалата част на пещта, т.е.. Д. Намаляване на размера на захранване е газ-въздушната смес и да се намали скоростта на флуидизиращия стойности достатъчно отдалечени от скорост Withania частиците.
За термодинамично равновесие nonoxidizing продукти на горенето в зоната на движение на проводника (температура> 600 ° С) горивен газ се извършва с липса на въздух (и при = 0.4) в присъствието на катализатор GIAP-3 зареден в чекмеджето с възглавница на инертни топки долу, предотвратяване на неговата карбонизация. зона на пещта I 1 М дълго катализатор отсъства.
Когато патентоването тел големи напречни сечения на камерата за охлаждане е необходимо да се разсее топлината. За тази цел, тук до нивото на кипящ слой прилага бобини със студена вода циркулира през тях. Тъй като според нашите инжекция лабораторни изследвания на водата директно в слоя осигурява още по-добър охлаждащ ефект, инсталираха и дюзи за разпръскване на вода, за да проверите охлаждането на изпарения при промишлени условия. Етапът между капачките в камерата за охлаждане е 70-75 мм. Нива на флуидите легла в двете камари са равни. За връщане корунд частици, увлечени от тел пещ в охладителна камера, образувана наклонени канали в преградата между камерите.
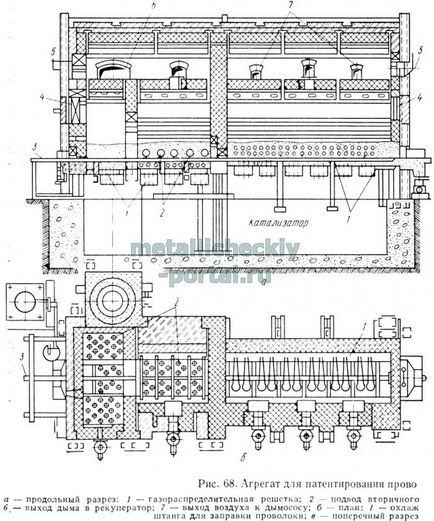
Доставката на флуидизиращото вещество в клетките се извършва секции равномерно по цялата ширина и дължина. Определени тел преминаване през външната единица сгъстен въздух на стените запечатва, което предотвратява изтичането на корунд частици навън. По проект всеки проводник нишка се въведе специален заключващ прът резба устройство, необходимо за изтегляне на тел от предната към задната стени на устройството; нишката след това се премества странично по протежение пълнеж пукнатини и се поставя в определена слот. И пещта и камерата за охлаждане са направени с две арки, пространството между които е димния.
Димните газове преминават от пещта на радиация рекуператора на предоставяне на топъл въздух, идващ след това към помощна доменна пещ и флуидизация в камерата охлаждане до 370- 510 ° С. Охладената отработените газове се изсмуква дихателен, при което вътрешността на устройството в пространството над кипящия слой се образува подналягане че премахва възможността за плюеше атмосферата газове в магазина.
За регулиране на основните процеси на автоматичен режим поддръжка и контрол на режима на устройството е снабдено с необходимите уреди.
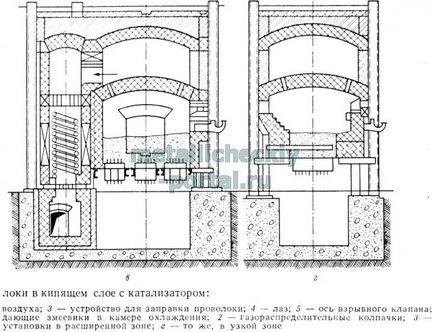
При монтаж единици със съответните средства за навиване и развиване, изчислени от 20 резба 5 часа От време на изпитванията все още не са заменени с капачки в страничните части на първата (разширен) региона, тези секции са положени тухли и ги разпенващ -. Увреждания. Чрез намаляване бяха проведени тестове топлинната мощност при скорост тел на 14.8 m / мин.
Устойчивост решетки с първите и вторите зони са съответно 13.4 и 11.3 кН / т2, когато устойчивостта на кипящия слой 0,6 кН / т2.
Резултатите от теста са показани по-долу. Те показват, че дори и 23%, което е над к. Н. Д. Patentirovochnyh конвенционалните пещи, въпреки че все още не достига на населеното място (40%) при тези неблагоприятни условия за изпълнение. Н. Г. пещ. Общо енергия. Н. D., Като се има предвид консумация на енергия и вентилатор вентилатор изпускателната (10 кВт в загряващата камера) е 22,1%.
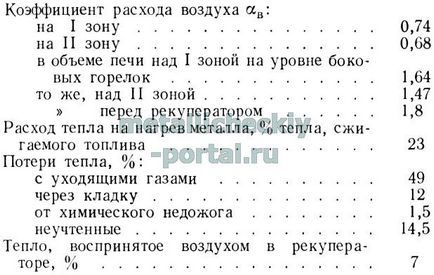
Големи загуби от отработените газове, значително по-високи от очакваното, са свързани с големи всмукателни чаши (по време на тестване на люка се отваря). Намаляване стойности на екран в пещта да позволи увеличаване на 1.1-1.15. N. D. Пещи до 26%.
Топлина на горещ въздух в. Н. Д. Не са включени, защото е било използвано за флуидизиране в камерата за охлаждане или взети в атмосферата. При използване на този топлообменник може да спести 7% гориво. Във всички експерименти, описани в камерата на пещта и охлаждане зарежда с (диаметър на частиците, съответно 200 и 100 микрона) алуминиев оксид. Режими са избрани, както е описано по-горе, когато се работи на три-резба.
Таблица. 23 показва, че при всички тествани условия, закаляване стомана 1H18N1 втвърдяване отстранена, темперирани якост на опън на телта по-ниска от 80 кгс / mm2, което отговаря на изискванията. Специални тестове в съответствие с ГОСТ 6032-58 показват, че във всички случаи на интеркристална корозия в темперирани тел липсва.
В микротвърдостта, измерена на инструмент PMTZ на под налягане 0,1 кгс, намалява с увеличаване на задържане време в кипящия слой, но всички експозиции е по-голяма, отколкото при нагряване в солна фурна за 40 минути, поради по-малко време отгряване.
Тестове, проведени за определяне на пластичност състав показаха, че тел темперирани в кипящ слой при скорост на 14.8 и 7.0 м / мин, както и на телта се темперира в солна баня, чертеж издържа без повреда до общо намаляване на 96 , 4% (до 0.48 mm). Няколко малки марж пластичност характеризиращ тел, темперирани при скорост 28,8 м / мин. Той се простира до диаметър от 0.51 mm (94.6% намаление).
Ханкс тел темперирани в кипящ слой, след като конвенционален подготовката на повърхността за рисуване (само бе изключен разхлабване операция шлака в стопилка сода каустик), за да отиде до магазина за съставяне нормалния маршрут в съответствие с намаляване на диаметър (мм): 2,50-2,05 -1,83-1,60-1,38- 1.20 при 120 м / мин. Рисунката се състоя без никакви усложнения.
По време на първоначалната настройка също се извършва 13 патентоване на стоманени телове нишки 60 с диаметър от 3.2 mm.

Свързани статии